Project study
Development of a small observation rocket for sample-return meteor dust
This project aims to sample the return of small meteoroid particles from space at an altitude of 100 km using a small sounding rocket. In particular, in the season of the year during which many small meteoroids hit the earth, we will be launching the sounding rocket simultaneously for sampling. Accordingly, a flexible launch of the rocket is also required.
In this study we design and develop a small sounding rocket that has high safety, low cost, and high response launching ability, reaching a height of 100 km. In addition, sea launch is selected for this project owing to the flexibility of the launch window. Currently, we use a small rocket to obtain basic data necessary for a sea launch experiment.
Click here to read more.
Development of a Kick Motor for Microprobe and Microsatellite
In our laboratory, we are developing two types of kick motors for microprobes: gas hybrid motors and solid motors.
We are conducting R & D on a completely new proprietary hybrid motor that combines Glycidyl Azide Polymer (GAP) and N2O (nitrous oxide). GAP is a polymer with high energy density and self-exothermic decomposition characteristics. By using GAP, we expect that “compact and lightweight”, “steady ignition”, and “large ΔV in a short time”, which are the requirements of kick motors for microprobes, can be achieved. The advantages of the hybrid rocket are that it can automatically extinguish the flame by stopping the oxidizer supply and it can be reignited later. Furthermore, GAP is not gunpowder and therefore has advantages in terms of safety, storage, and export. On the other hand, nitrous oxide, which is used as an oxidizer, does not need to be cooled, such as liquid oxygen, and easy to handle for satellite loading. If nitrous oxide, an oxidizer, is absent in the tank, cold gas jets can be used.
We have already succeeded in the ground combustion test of the GAP/N2O gas hybrid rocket in our laboratory, and are now proceeding with the design and combustion experiment of the flight motor. In the previous design study, the maximum ΔV was 1020.7 km/s when the GAP/N2O gas hybrid motor was used for 3U of the 6U size microprobe. On the other hand, the maximum ΔV was 531.4 m/s when the GAP/N2O gas hybrid motor was used for 10 kg of the 50 kg Microsat probe. All of these are sufficient speeds to control the orbit of a microprobe. For example, it is possible to change the orbit altitude of a lunar orbiter, fly to the moon from the stationary transition orbit (GTO), or even escape the Earth’s gravitational sphere and reach deep space. It is also a propulsion system that can be expected to enter the Martian transition orbit from the manned lunar base Gateway and the HTV-X for the gateway supply.
We are also developing a solid rocket motor based on GAP as a more compact kick motor than a gas hybrid. Solid-state rockets have a simple and compact mechanism that can only be burnt once; however, they are characterized by strong acceleration. By using GAP with high energy density, even a 1U size motor which is 10 cm × 10 cm × 10 cm cubic units can achieve a sufficient acceleration of 381 m/s for the orbit maneuver of a 3U cube sat size probe. Because of its ultra-small size, it can meet the needs of various missions depending on its ingenuity, such as orbit insertion, de-orbit, and landing, which are used by installing multiple units and dividing them into phases.
Click here to read more.
Research
In this laboratory, we mainly conduct research on hybrid rockets based on the study of propulsion and combustion engineering. We are developing excellent fuel for hybrid rockets, investigating the combustion mechanism, proposing new propulsion systems, and demonstrating small rockets in flight experiments. Moreover, we are engaged in extensive activities from basic to applied, including the development of new solid propellants, the construction of combustion models, and basic research on new oxidizers.
Hybrid Rocket Combustion Experiment
Fuel regression rate measurement
Thrust 100 N, 500 N, and 1500 N class combustion experiments
Hybrid rockets use plastics as fuel; therefore, they are considered to be a highly safe and low-cost propulsion system. On the other hand, the fuel regression rate, which is the fuel combustion speed, is low, and it is difficult to increase the thrust. Therefore, in our laboratory, the fuel retraction rate is measured using a hybrid rocket motor of various sizes, and their characteristics are investigated.
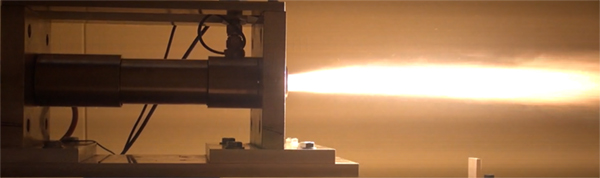
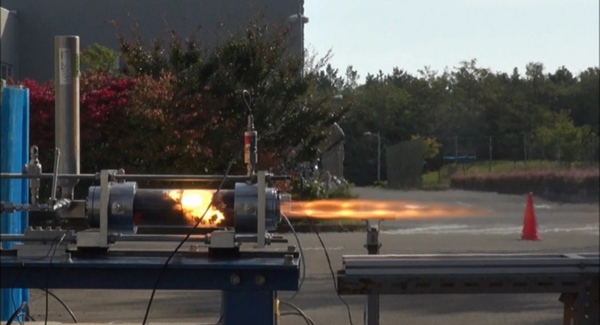
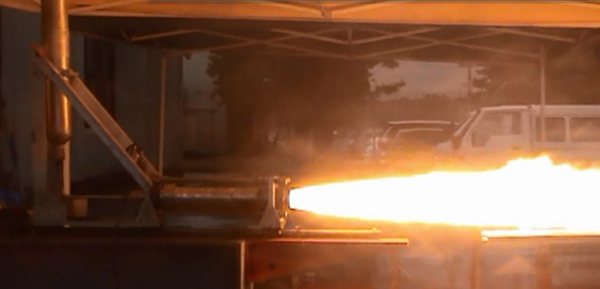
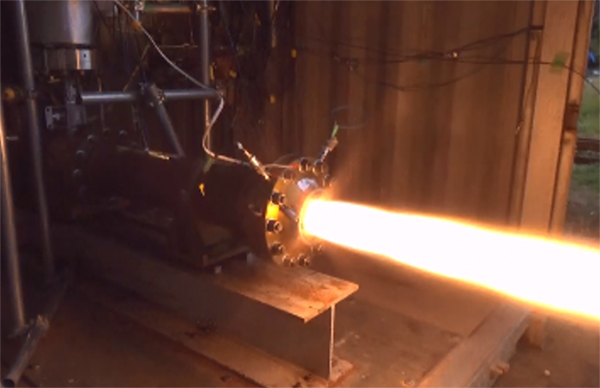
Combustion experiment using a swirl flow system
We know that the fuel regression rate increases by applying a swirl flow to the oxidizer. Therefore, we are conducting research on changes in the fuel regression rate when a low-melting thermoplastic fuel under development in our laboratory is applied to the swirl flow of the oxidizer. We plan to apply this technology for thrust control under optimum conditions and to burn fuel uniformly.
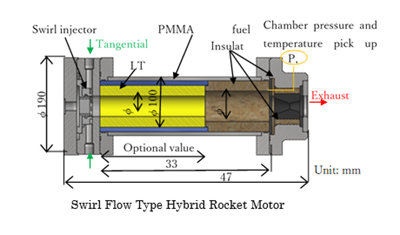
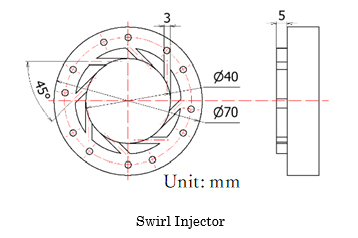
Gas hybrid rocket
In a gas hybrid rocket, the fuel is gasified and mixed with an oxidizer to burn. In this research, we propose and demonstrate a direct injection-type gas hybrid rocket that decomposes itself by using a high-energy material as fuel and simultaneously injects an oxidizer into the motor.
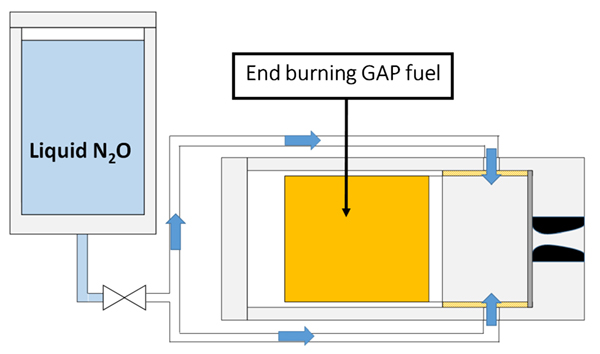
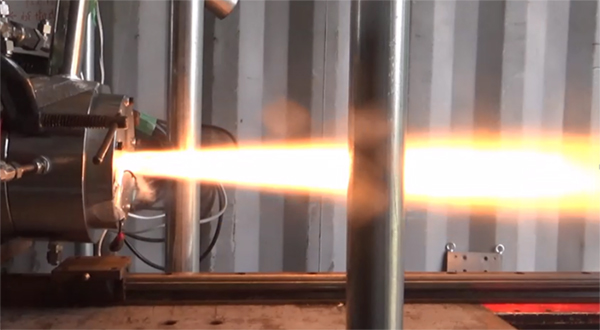
Visualization of combustion flame and measurement of temperature profile inside fuel
A combustion chamber with an observation window is used to observe flames during combustion in a hybrid rocket fuel experiment. Flame visualization is difficult because of the high pressure of 2 MPa during combustion. However, our laboratory has succeeded in obtaining clear images and we are able to observe flames for various fuels. At the same time, a thermocouple with a wire diameter of 25 μm inside the fuel was inserted, and the temperature history inside the fuel during combustion was successfully obtained. Combining these technologies, we aim to establish the combustion mechanism of hybrid rocket fuels that burn in high-temperature and high-pressure environments.
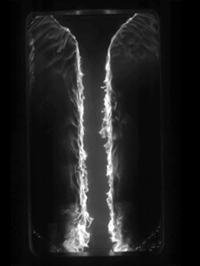
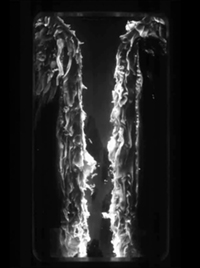
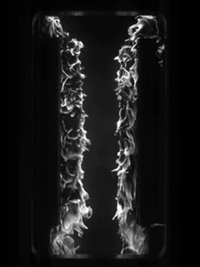
Small hybrid rocket launch experiment.
We are conducting an experiment to launch a hybrid rocket at an altitude of 200 m in Onjuku Town, Chiba Prefecture, with the aim of providing practical education for university students. The first launch was conducted from a floating launch pad, and in March 2019, Japan’s first sea launch experiment was successfully conducted.
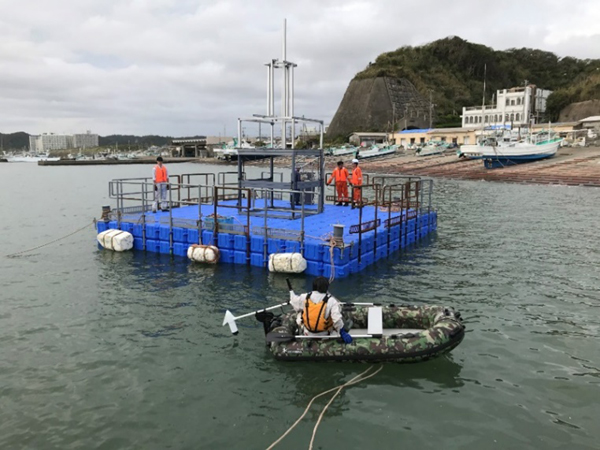
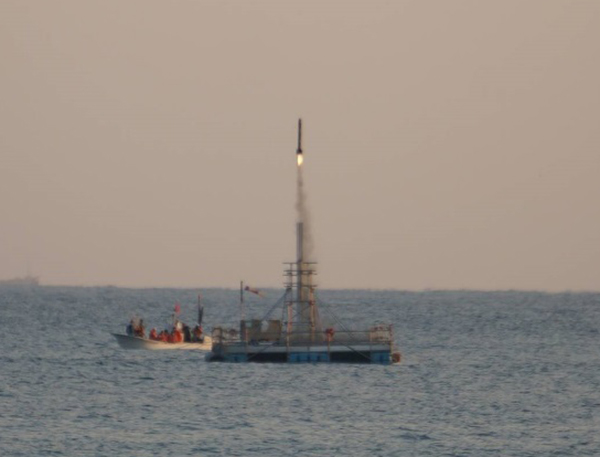
As a demonstration experiment of the low-melting-point thermoplastic fuel (LT fuel) developed in this research, we carried out a launch experiment of a 1.5 kN-class thrust hybrid rocket at Izu Oshima in July 2016. The rocket was launched at supersonic speed and attained a maximum altitude of 4889 m in 23 s, demonstrating that LT fuel burns normally even in an acceleration environment.
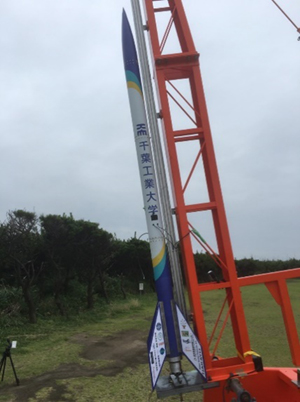
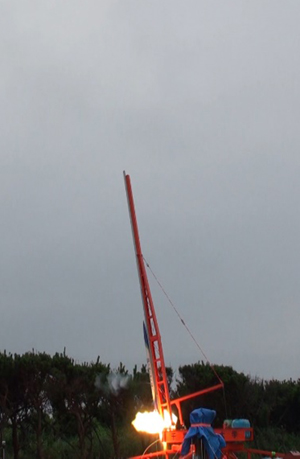
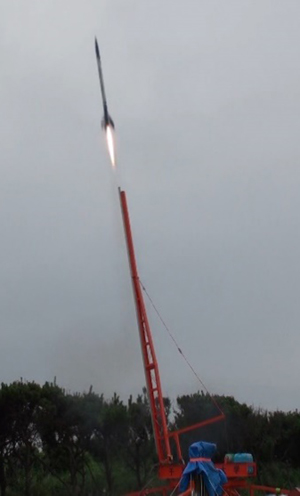
Other research
- Development of new fuel for hybrid rockets
- Acquisition of mechanical properties
- Evaluation of the feasibility of the structure
- Rapid thermal analysis
- Combustion simulation
- Proposal of new solid propellants
- Higher performance due to high-energy materials
- Non-debris generation
- Elucidation of the decomposition mechanism of nitrous oxide
- Evaluation of Self-Heating Decomposition Characteristics
- Catalytic effect
——————————————————————————————————
Yutaka Wada
yutaka.wada(at)p.chibakoudai.jp
Chiba Institute of Technology (Chitech),
Tsudanuma 2-17-1, Narashino, Chiba 275-0016, Japan
tel.+81-47-478-4734, fax.+81-47-478-0372
——————————————————————————————————